Injection Molding Manufacturing: Revolutionizing the Metal Fabrication Industry
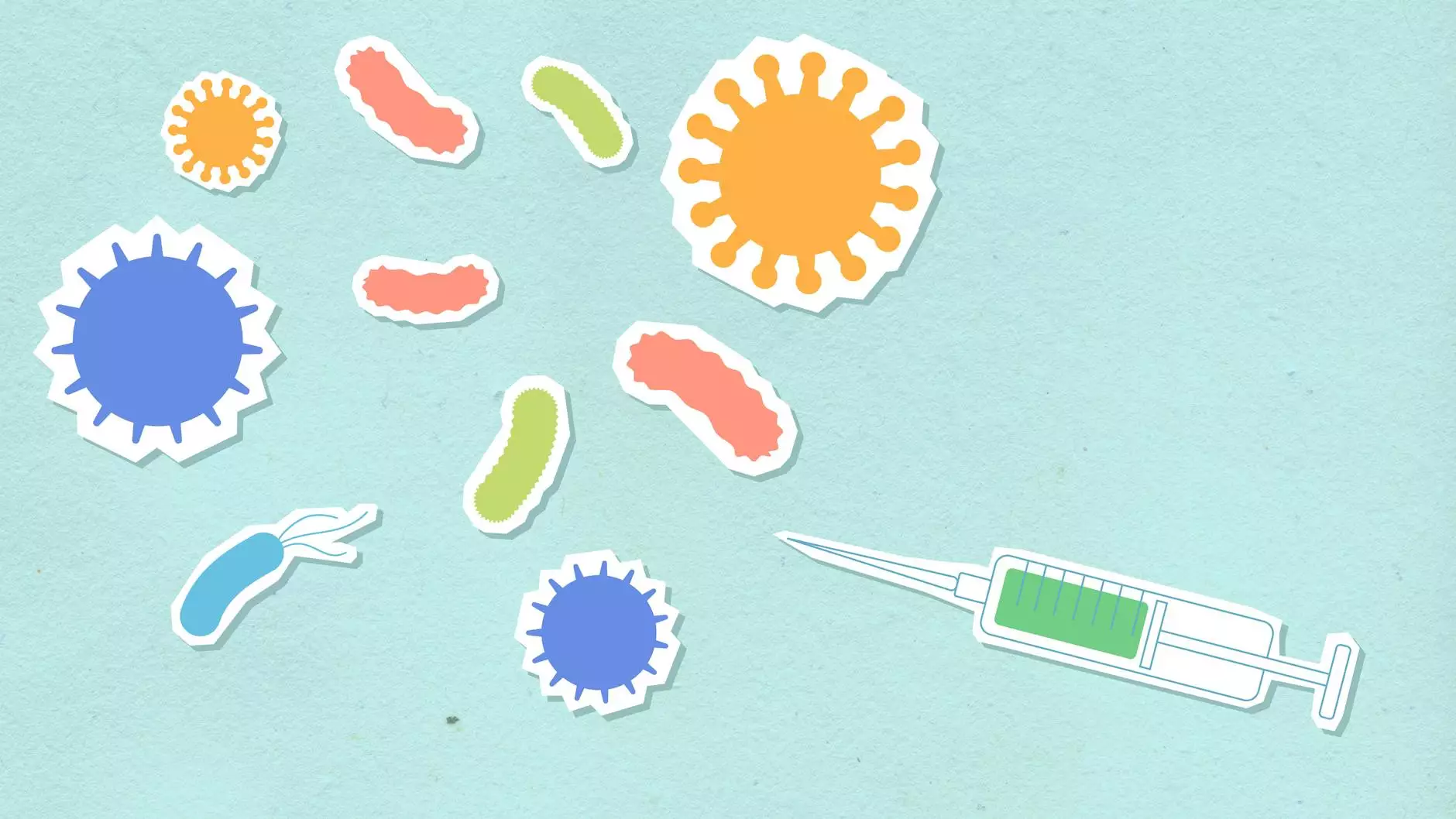
The landscape of injection molding manufacturing has seen remarkable growth and innovation, especially within the realm of metal fabricators. This article delves into the intricacies of injection molding, its various benefits, and how it can transform your business operations.
What is Injection Molding?
Injection molding is a manufacturing process that involves injecting molten material into a mold, where it cools and solidifies into a specific shape. This method is widely used for producing both plastic and metal components, making it a versatile solution for industries ranging from automotive to consumer goods.
The Role of Injection Molding in Metal Fabrication
In the metal fabrication sector, injection molding is employed to create intricate and durable metal parts. This method provides numerous advantages over traditional manufacturing techniques.
Benefits of Injection Molding Manufacturing
- High Precision: Injection molding allows for a high degree of accuracy, ensuring that every part produced meets strict tolerances.
- Cost-Effective Production: Once the initial mold is created, the cost per unit decreases significantly, making it economically feasible for large-scale production.
- Fast Production Rates: The injection molding process is capable of producing parts quickly, which is vital for meeting demand in fast-paced industries.
- Complex Geometries: This method can produce intricate shapes and designs that would be difficult or impossible to achieve with other methods.
- Material Versatility: While primarily associated with plastics, advancements in injection molding technology have made it possible to use various metals and alloys.
How Injection Molding Works
The injection molding process involves several key steps, ensuring that the final product meets specifications and quality standards:
Step 1: Design the Mold
The first step in injection molding is designing the mold. This involves careful consideration of the product's dimensions, features, and the material to be used. CAD software is often utilized to create precise mold designs.
Step 2: Material Selection
The choice of material is crucial. For metal injection molding, powdered metal is commonly used. It is blended with a binder that allows easy handling. When heated, the binder melts, and the metal powder can be injected into the mold.
Step 3: Injection Process
During this phase, the molten metal is injected into the mold under high pressure. This process ensures that the material fills every cavity of the mold, creating a dense and uniform part.
Step 4: Cooling and Solidification
After injection, the part is allowed to cool. This timing can vary depending on the material and the complexity of the design. Cooling too rapidly can lead to defects, so temperature control is essential.
Step 5: Ejection
Once adequately cooled, the mold opens, and the finished part is ejected. This step needs to be performed carefully to avoid damaging the part.
Step 6: Finishing Touches
After ejection, parts may require additional finishing processes like machining, coating, or heat treating to achieve the final desired properties.
Applications of Injection Molding in Metal Fabrication
Injection molding is employed in various applications, showcasing its versatility and effectiveness:
- Automotive Components: Parts such as gears, brackets, and housings that require high strength and durability.
- Consumer Electronics: Production of high-precision components like casings for smartphones and laptops.
- Medical Devices: Manufacturing complex parts for medical instruments that require uncompromised quality.
- Aerospace Components: Creating lightweight yet robust components that meet stringent safety standards.
- Household Items: From small metal utensils to home appliances, injection molding caters to various consumer needs.
Choosing the Right Injection Molding Partner
When considering an injection molding manufacturing partner, there are several factors to evaluate:
Experience and Expertise
Look for a company with a proven track record in injection molding manufacturing. Experience in your specific industry can be a significant advantage.
Quality Assurance
A reliable partner should have stringent quality control measures in place. Certifications like ISO can indicate a commitment to quality.
Technology and Innovation
Choose a company that utilizes the latest technology in injection molding. Innovative practices can improve efficiency and end-product quality.
Customer Support
Effective communication and support during the production process are essential. A responsive partner can resolve issues quickly and adapt to changes as needed.
The Future of Injection Molding Manufacturing
As technology evolves, so too does the field of injection molding. Key trends shaping the future include:
Automation and Robotics
Incorporating robotics into the production process can enhance efficiency and reduce labor costs. Automation helps streamline operations, allowing for faster production cycles.
Sustainability Initiatives
With environmental concerns at the forefront, many companies are seeking sustainable practices within injection molding manufacturing. This includes using recyclable materials and reducing waste during production.
Advanced Materials
New developments in materials science are expanding the horizons of what can be achieved with injection molding. Innovations in metal alloys and composites may lead to even lighter and more robust components.
Conclusion
Injection molding manufacturing stands as a cornerstone of the metal fabrication industry. Its ability to produce high-precision, cost-effective components rapidly has made it a favored choice among manufacturers. As trends in automation, sustainability, and advanced materials continue to reshape the landscape, partnering with a skilled injection molding specialist is more crucial than ever for businesses aiming to stay competitive.
By embracing these innovations and understanding the injection molding process, metal fabricators can not only improve their production capabilities but also enhance the quality of their products, ultimately solidifying their position in the market.
For businesses looking to explore the potential of injection molding, working with experienced partners like DeepMould.net can unlock new opportunities for growth and efficiency.