Understanding Injection Molding Tool: Innovations and Applications
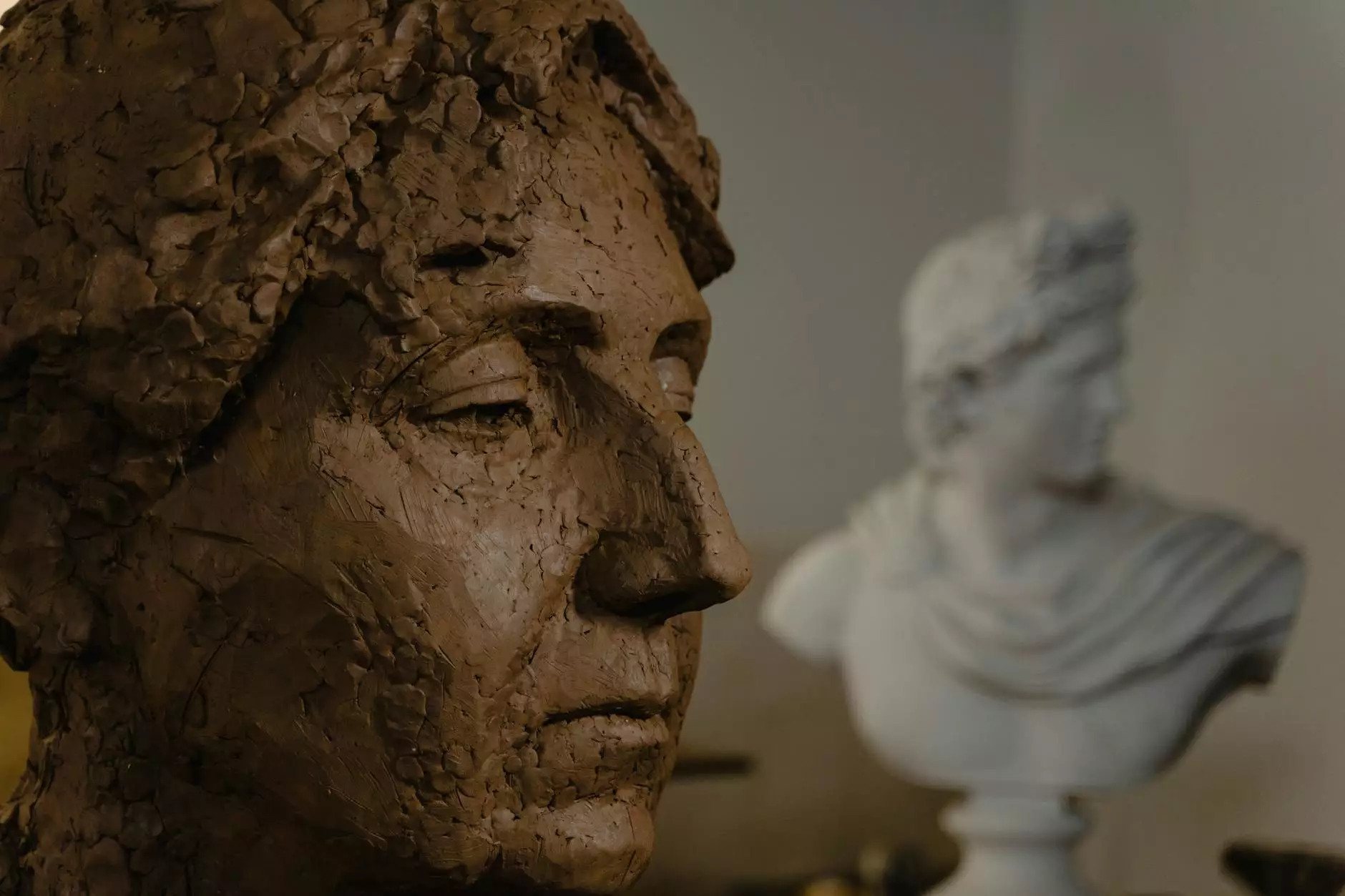
Injection molding tools play a pivotal role in the industrial sector, especially for companies specializing in metal fabrication. These tools are essential for producing a wide range of components efficiently and with excellent precision. This article provides an in-depth look at injection molding tools, covering their functionalities, types, benefits, and best practices for use in the industry.
What is an Injection Molding Tool?
An injection molding tool is a specialized device used to create parts by injecting molten material into a mold. The process is highly regarded for its ability to produce parts with intricate shapes and fine details, making it ideal for various manufacturing applications. The molds are typically made from high-quality steel or aluminum to withstand repeated use and maintain their shape under high temperatures and pressures.
How Injection Molding Works
The method of injection molding involves several critical steps:
- Material Selection: The first step involves selecting the appropriate material, often thermoplastics or thermosets, based on the desired characteristics of the final product.
- Melting the Material: The chosen material is fed into a heated barrel where it is melted and prepared for injection.
- Injection: The molten material is injected into the mold cavity under high pressure, ensuring that it fills every part of the mold.
- Cooling: Once the cavity is filled, the material is allowed to cool and solidify, acquiring the mold's shape.
- Ejection: Finally, the mold opens, and the completed part is ejected from the tool.
Types of Injection Molding Tools
There are several types of injection molding tools, each serving different manufacturing needs:
- Conventional Injection Molding: This method uses a single mold to create multiple parts, suitable for high-volume production.
- Multi-Cavity Molding: This type has more than one cavity per mold, doubling or tripling production rates.
- Family Molding: Family molds produce multiple parts of different shapes in a single cycle, enhancing efficiency.
- Insert Molding: Here, metal or other parts are molded into the plastic component, which is perfect for applications requiring assembly of multiple materials.
Benefits of Using Injection Molding Tools
Implementing injection molding tools in production processes offers numerous advantages:
- High Efficiency: Once the mold is created, parts can be produced rapidly, leading to reduced cycle times and enhanced productivity.
- Precision and Consistency: Injection molding provides high precision in part dimensions and ensures that all produced items meet stringent quality standards.
- Material Versatility: A wide range of thermoplastics and thermosets can be utilized, enabling manufacturers to select the best material attributes for their applications.
- Reduced Waste: The process minimizes material waste, as any surplus material can often be recycled back into the system.
- Complex Designs: Injection molding allows for intricate designs that would be difficult or impossible to achieve through other manufacturing methods.
Applications of Injection Molding Tools
Injection molding tools are applied across various industries, thanks to their adaptability:
1. Automotive Industry
Injection molding plays a significant role in the automotive sector by producing components such as dashboards, panels, and exterior parts. Its ability to create lightweight yet durable components is essential for improving fuel efficiency and performance.
2. Consumer Goods
From toys to kitchen appliances, many consumer products are manufactured using injection molding tools. The versatility in design options allows companies to create unique products that stand out in the market.
3. Medical Devices
The medical field relies on injection molding for producing precision parts that comply with rigorous standards. Devices like syringes, casings, and complex surgical instruments often utilize these manufacturing techniques to ensure safety and reliability.
4. Industrial Applications
Industrial components such as housings for equipment, switches, and connectors benefit from the strength provided by injection molded parts.
Choosing the Right Injection Molding Tool Provider
When selecting a provider for injection molding tools, there are several factors to consider:
- Experience: Look for manufacturers with a proven track record in the industry, particularly ones with expertise in metal fabrication.
- Technology: Evaluate whether the provider uses the latest technology in tool design and manufacturing processes, which can greatly affect quality and lead times.
- Customization: Ensure they offer tailored solutions to meet your specific requirements, minimizing additional costs in later production stages.
- Quality Assurance: Check if the company follows stringent quality control measures to guarantee the highest quality of parts produced.
Conclusion
In conclusion, the importance of injection molding tools cannot be understated in today’s manufacturing landscape. They enable companies, like those associated with deepmould.net, to produce high-quality, intricate parts efficiently and effectively. By utilizing advanced techniques and focusing on technological advancements in metal fabrication, manufacturers can stay ahead in the competitive market, ensuring they meet the growing demands of various industries.
Final Thoughts
Investing in state-of-the-art injection molding tools and working with reputable providers can significantly enhance production capabilities. As industries continue to evolve, so will the methods and technologies associated with injection molding. Staying informed and adapting to these changes is essential for any business looking to thrive.